Quality Control
Home » Quality Control
Quality Control
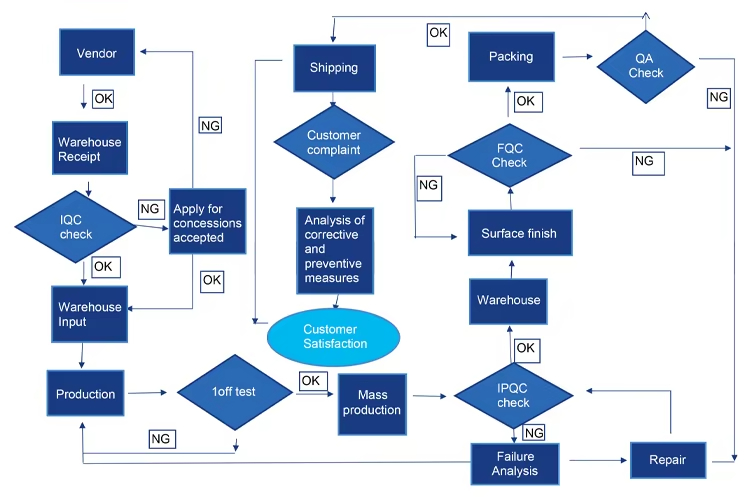
Controlling the quality of CNC (Computer Numerical Control) machined parts is crucial to ensuring that the final product meets the required specifications, performs well, and functions as intended. Here are key strategies for quality control in CNC machining:
1. Material Selection and Inspection
- Material Specifications: Ensure that the raw materials meet the required standards for the project.
- Visual Inspection: Inspect the material for defects such as cracks, warping, or inconsistencies before starting the machining process.
- Certificate of Conformance (CoC): Always request CoCs for the raw material from the supplier to verify that it meets the necessary specifications.
2. Machine Calibration and Maintenance
- Regular Calibration: Ensure that the CNC machine tools are regularly calibrated to maintain accuracy. This includes checking the alignment of axes, spindle, and other key components.
- Preventive Maintenance: Perform routine maintenance, such as lubrication, cleaning, and checking machine parts for wear. This reduces the risk of errors during machining.
- Machine Temperature Control: Maintain a stable temperature to prevent expansion or contraction of parts and tools, which can lead to dimensional errors.
3. Tooling Control
- Tool Inspection: Regularly check tools for wear, damage, and accuracy. Worn-out tools can cause dimensional inaccuracy or surface finish problems.
- Tool Offset Setting: Ensure correct tool offset settings before starting a new machining operation to prevent deviations from the desired dimensions.
- Tool Changing Schedule: Establish a schedule for tool replacement or re-sharpening, based on the material being machined and the type of operation.
4. Process Control
- Program Verification: Verify the CNC program (G-code) for accuracy before execution. Use software simulations or dry runs to check for potential issues.
- Cutting Parameters: Use appropriate cutting speeds, feeds, and depths of cut. Improper settings can lead to poor surface finish, dimensional inaccuracies, or tool damage.
- Chip Removal and Cooling: Use effective chip removal methods and coolant management to avoid issues like overheating, poor surface finish, or tool wear.
5. In-Process Inspection
- Dimensional Control: Use precision measuring instruments (e.g., calipers, micrometers, and height gauges) to check key dimensions during the machining process.
- Runoff Parts: For complex parts, inspect a sample piece after each tool change or after a set number of parts to ensure consistency.
- Surface Finish: Check the surface finish using roughness testers or visual inspection, especially for critical surfaces.
- Coordinate Measuring Machines (CMM): For high-precision parts, use CMMs to check the part’s dimensions and geometry against the CAD model.
6. Post-Process Inspection
- Final Dimensional Check: After the machining process is complete, thoroughly inspect the part for any deviations in size, shape, or features.
- Quality Control Checklist: Implement a checklist for final inspection that includes checks for burrs, sharp edges, surface finish, and geometric tolerances.
- Hardness and Material Testing: Conduct tests such as Rockwell hardness testing if material properties are critical to the part’s performance.
7. Documentation and Traceability
- Recording Measurements: Maintain a log of key dimensions and quality checks throughout the process for traceability.
- Inspection Reports: Ensure that all inspection results, including material certificates, tool measurements, and final inspection reports, are documented and stored properly.
- Non-Conformance Reporting: If a part doesn’t meet quality standards, document the issue and conduct root cause analysis to prevent recurrence.
8. Employee Training
- Operator Training: Ensure that CNC operators are properly trained in machine operation, programming, and quality control procedures.
- Awareness of Tolerances: Teach operators the importance of tight tolerances and how to achieve them, reducing human error and improving part consistency.
9. Feedback and Continuous Improvement
- Review and Correct: Regularly review the quality control results and identify areas for improvement, whether in processes, tooling, or machine settings.
- Customer Feedback: If possible, get feedback from customers about part performance, which can provide valuable insights into potential quality improvements.
- Root Cause Analysis: For any quality issues, perform root cause analysis (such as 5 Whys or Fishbone diagram) and implement corrective actions.